The Lost Art of Technology Innovation in the Process Industry
The push for greener products and processes is leading many companies to introduce new technology or new feedstocks to existing processes. While everyone recognizes that implementing first of a kind technology poses risk, most companies do not have the experience to understand the magnitude and consequences of these risks and lack the systematic technology maturation process and associated governance to mitigate them. IPA has seen companies with deep commercialization expertise and routine deployment of new technology in the 1980s and early 1990s gradually lose this capability during the 25 years that followed.
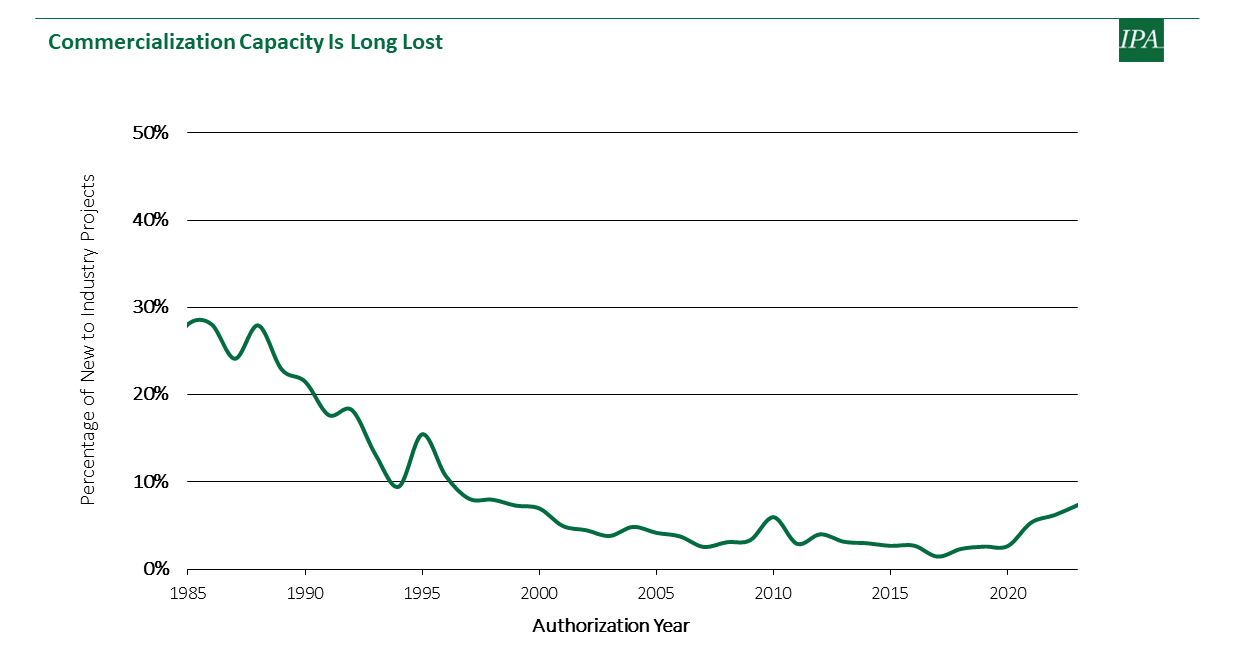
In addition to lack of experience and inadequate governance, new technology projects often suffer from a combination of insufficient resources, undue schedule pressures (driven by the desire to be first to market), and reputational pressures from promises made to shareholders. The recent uptrend in the deployment of new technology combined with the lost art of commercialization sets up the potential for costly mistakes and puts the decarbonization transition at risk.
An additional challenge to the emergence of new process technologies is the desire (and suggestion by many consultants) to leverage processes used in the recent success of information technology (IT) innovations for the deployment of new industrial process technologies. Although some practices might apply, by and large using the framework in its entirety is not appropriate and will lead to failure. Unlike IT projects that may be able to release a product and fix bugs or update functionality afterwards, spending tens or hundreds of millions of dollars on a commercial process plant that does not operate with the plan to fix bugs or change functionality is a disastrous approach to innovation. All of these attempts in our database led to facilities with extraordinary costs and durations to fix in the best cases—and total walkaways and/or industrial accidents in the worst cases. IPA’s mantra is to, “Make your mistakes on a small scale and make your money on a large scale.”
What works in the process industries? IPA has evaluated the implementation of first of a kind technology in more than 1,000 commercial process projects and identified the Best Practices required to have a successful new technology process at a commercial scale.
A recent IPA article outlined some of the organizational, work process, and governance requirements that companies need to follow to commercialize new technology projects. These are foundational elements for success focused on the organizational side of commercializing innovative processes. To be successful, we also need to know the Best Practices for the technical side of innovation in terms of the piloting pathway for any new technology process. This article discusses some of the technical dimensions of industrial process technologies that affect the development and piloting pathway needed to commercialize new-to-industry technology. Underpinning this framework is the finding that the development pathway needs to be built around the nature of the new technology and employing the wrong approach (e.g., the IT development framework) will lead to failure.
Process Attributes Determine Best Practices for New Technology Process Development
The need for piloting and the nature of the piloting requirements are major considerations that balance development time and costs versus the risks of having an unsuccessful commercial plant. The process can range from piloting of individual unit operations that often focus only on the new step or steps being introduced into a process up to a fully integrated pilot plant that, apart from scale, matches the commercial process. The differences in piloting approach have large implications on the time and cost of development. Knowing when an integrated pilot plant is required and when it is not, is critical to getting it right.
Through researching new technology projects in our project database, we have found several attributes of the process that help frame the need for a particular piloting pathway. The goal of having a commercial plant that can operate 24/7 and consistently produce on-spec products within an economic envelope that makes the plant profitable requires a development and piloting process that is appropriate to the technology. Sometimes, there is neither the appetite for the time and cost required to go through a potentially lengthy development phase nor an understanding by R&D of what is required to get to a commercially viable plant.
Below we present four attributes that have consistently shown up in our data to drive a need for more extensive piloting. There are several other attributes that contribute to piloting requirements, but those are more nuanced. The key is to match the piloting approach to the technology and nature of state of the materials.
Process Complexity
The first is the complexity of the process. Although this seems obvious, it is often not considered when the piloting plan is developed. IPA defines complexity as the number of continuously linked process steps that include a reaction, separation, or change of phase. IPA found there is a complexity count above which skipping an integrated pilot plant leads to major issues with, or outright failure of, the commercial plant. In contrast, simple processes and batch processes that have breaks between the process steps have a lower need for an integrated pilot plant. Bypassing the integrated pilot plant when it is needed often leads to protracted startup times for trouble shooting and major additional capital (fix it projects) to correct or modify the plant. In some cases, the commercial entity has been a walk away that did not produce a single unit of saleable product.
Number of New Steps
A second attribute is the number of new steps (commercially unproven process steps) included in the overall process. The addition of each new process step creates additional uncertainty in the overall process. As with process complexity, there is a threshold of new process steps that, when exceeded, indicates the need to use an integrated piloting approach. As shown below, the number of new steps increases the time required for startup of a commercial plant and the actual operational performance is, on average, far lower than expected as the number of new process steps increases. Note, the graph only includes projects that actually did start up—those that never reached steady state operations (i.e., infinite startup duration) could not be included in the averages.
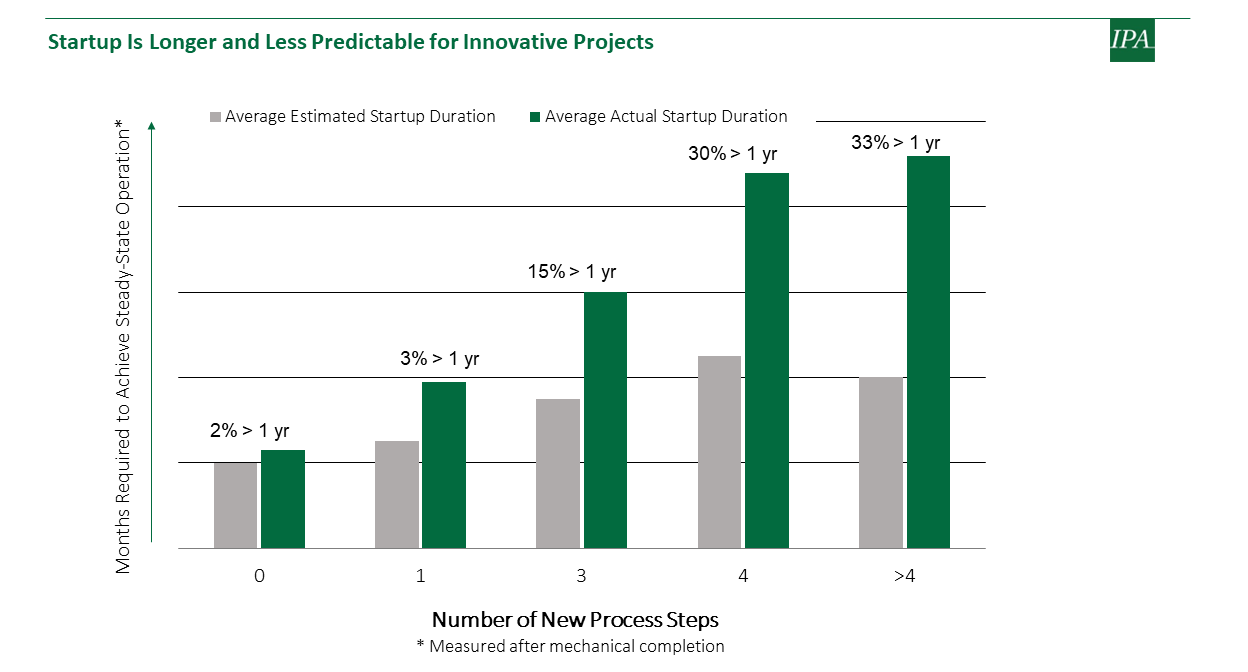

Intermediate Recycle Stream
Another attribute that informs the piloting pathway is the presence of an intermediate recycle stream; this is further complicated if there are also impurities. Processes that have a recycle stream create the possibility of buildup of impurities or side products over time. The implications of these on the operation of the process cannot always be anticipated from piloting a once-through unit operation step. The addition of a recycle stream, particularly if there are impurities, is another attribute that informs the need for an integrated pilot process that includes the recycle stream as well as sufficient continuous operation of the pilot process to understand the effects of the recycle stream on the steady state operation of the process.
Feedstock
A fourth attribute that informs the piloting pathway is the feedstock state. Feedstock that is a solid creates more uncertainty in technology development and scale-up than feedstock that is a liquid or gas. Although a lot of attention is given to the chemistry, the processing of solids and other problematic feeds and intermediates (slurries and non-Newtonians) is difficult to model and therefore anything more than a modest scale-up can result in problems like bridging, plugging, erosion, and channeling. In addition, raw solid feeds (e.g., run of mine or agricultural/forest waste) create an additional dimension from the variability in the feed itself. Piloting is needed to comprehend the variations in the feed. Often times, piloting with a limited sample of the feed leads to surprises during operation of the commercial plant when the feed has variations not seen in the pilot operation (size, shape composition, impurities, moisture, etc.). Again, an integrated pilot process that is run with representative samples of feed and includes enough run time is required to fully understand the effects on the design and operational parameters of the process.
How IPA Can Help
Understanding these four attributes of the technology is critical to identifying the basic technical data required to design a functioning commercial operation, and consequently informs the design of the pilot facility and, equally importantly, the type and extent of piloting activities. IPA’s New Technology Commercialization Workshop is designed to identify and characterize these attributes, along with other more nuanced attributes, and help design an ideal commercialization path that balances resources and probability of success according to a company’s risk appetite. The workshop also provides key stakeholders with an understanding of the organizational requirements specific to the technology and quantitative benchmarks from the effects of the new technology on cost, schedule, and early operational performance. This information is imperative to balance the risks of different choices for commercialization and piloting approaches and to navigate the commercialization path.