A Changed Landscape for the Chemicals & Petrochemicals Industry
These are challenging times for the Chemicals Industry. Access to new sources of low cost feedstock has led to an increase in capital project activity, especially in the United States. Companies have authorized large capital investments—some the largest in a company’s history—to take advantage of opportunities. Executing large capital projects is always challenging, but it is evident today that many companies have underestimated the complexities of the current supply chain for capital projects.
To cope with increased project market risks and business pressure, project teams in recent years have increased the conservatism of their project cost targets. As a consequence, the Chemicals Industry has recently lost its competitive edge against its peers in the capital projects industry when it comes to spending capital effectively. It was not so long ago that the rest of Industry looked up to the Chemicals Industry as the standard bearer for delivering cost effective projects. Chemicals projects are giving up 10 to 15 percent more capital than they were 10 years ago. This is a serious issue for an Industry where capital effectiveness is an historical imperative. For chemical companies, capital effectiveness is vital to long-term success, i.e., protecting narrow business profit margins and gaining or preserving market share.

To gain a better perspective of the challenges facing Industry, it is important to take a step back to consider how the projects world has changed over the last decade.
Whereas businesses worried 10 years ago that their project teams were understaffed, many today are focused on headcount reductions. By the same token, chemical companies were ordinarily able to find experienced engineers and project managers to work on projects a decade ago. Today, it is more difficult to find the same levels of talent. IPA data show that chemical companies have less collective team experience as a whole relative to the past or even to other industrial sectors. Demographic challenges are partly to blame and so is the unwillingness of many owner companies to retain core project competencies. Specifically, owners have lost essential capability in cost engineering, construction management, and project controls.
Declining Labor and Engineering Productivity
Similarly, the quality of engineering, procurement, and construction (EPC) contractors specific to the management and execution of capital projects was much stronger a decade ago. The current engineering quality level is the poorest the Industry has ever seen. The error rate on engineering drawings from engineering contractors has increased by over 50 percent since 2006. The decline in engineering quality makes it difficult to achieve planned schedules. IPA’s data show that more than 80 percent of chemical projects start to slip their schedules in engineering. The average chemical project slips the estimated date for completing detailed engineering by 32 percent. Such slip creates an almost equal delay in the overall project completion. Engineering packages either do not arrive in the field on time or contain errors or both. Construction plans need to be reworked, and construction work is done out of sequence. This results in labor productivity losses and construction rework, which, in turn, result in schedule delays and cost growth. A project that slips engineering by 30 percent or more usually suffers 5 to 10 percent overall cost growth because of the effect on the construction.
Moreover, a decade ago, many businesses understood that to be competitive, some projects in the portfolio would overrun their targets; today, they appear to be much more risk averse and place greater value on predictability. This shift of focus is a manifestation of businesses’ limited understanding of estimate progression and its accuracy ranges at different stages of project development. The end result is very conservative authorization estimates.
To make matters worse, many chemicals companies have lost the ability to effectively control project execution in the field. Experienced construction managers and project controls professionals are in short supply. Poor physical progressing of engineering and field activities make it difficult to be able to truly measure progress and understand project status and risks ahead and develop mitigation plans.
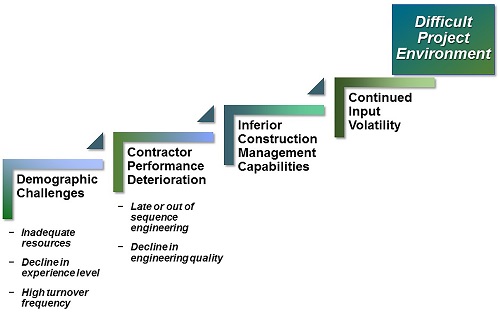
IPA sees these trends reflected in the project benchmarks. These less experienced project teams take longer to conduct project definition, and the quality of project planning and definition work for the average chemical project has declined significantly, essentially falling to the level of other industrial sectors. The product of the project definition phase is an estimate that is more conservative than historical norms, indicating a level of compensation for the limitations and uncertainty. Incomplete project definition and planning combined with lower EPC contractor capabilities and a weaker owner control function drives a much higher chance of project cost growth and schedule slip.
How to Improve Project Organizational Systems and Capabilities
To respond to the challenges facing projects today, the Chemicals Industry must begin focusing on a few key areas for improving their existing organizational systems and capabilities. Stronger systems need to focus on maintaining their capabilities, while weaker ones need to devote time and resources to building (and in some cases re-building) owner strength in core competencies and processes. Unfortunately, many companies today report that they are ill prepared to deal with resource shortages. IPA’s recent survey of over 25 chemical companies shows that one in two believe their company does not currently employ people with the right skill sets or experience, especially for project controls, estimating, and construction management. An additional 30 percent believe companies cannot buy these skills on the market place.
This means intensive in-house training is paramount to improve project performance. IPA’s data show that additional training pays off handsomely as better trained teams achieve better project definition at authorization and deliver better projects. However, only 30 percent of the respondents had plans in place for training and mentoring. Another 20 percent planned to rely on contractors to do the work, and the remaining 50 percent were not aware of any formal company programs to address the issue.
There’s no turning away from what the data show; the projects market has changed. If the Chemical Industry wants to get serious about regaining its position as the leader in delivering capital effective projects, companies need to focus on strengthening their project teams and system capabilities.